If you are working in textile manufacturing, we are sure you might have heard about silicone defoamers you would know how foam-related issues can affect your textile manufacturing process. And all these lead to inefficiencies and poor-quality output!
But let us tell you – you are not alone! Many many textile manufacturers face challenges like foam buildup during the processes of dyeing, washing, and finishing – harming their overall production cycle.
Does this mean there is no solution for this? Well, not really!
To overcome the challenge of foaming, you can leverage the magic of silicone defoamers. As silicone defoamers are known for their superior performance and amazing properties, the demand for silicone defoamer manufacturers in India is growing day by day!
So, if you are new to the concept of silicone defoamers, we’ve got you covered!
In this blog, we’ll explore the benefits of silicone defoamers, why choosing the right silicone defoamer manufacturers in India is important, and how the silicone defoamer price impacts your overall production costs.
Let’s get started by understanding silicone defoamer in the context of textile manufacturing
- What is a Silicone Defoamer?
Simply put, silicone defoamer is a specialized chemical agent designed to reduce or eliminate foam formation in various industrial processes, particularly in textile manufacturing.
As silicone defoamers have siloxane-based compounds, they are quite effective not only at breaking down the foam but also at the new foam.
With key ingredients such as silicone oils, emulsifiers, and other additives, silicone defoamers can efficiently tackle the issue of excessive foam in textile production.
When you prevent the foam formation from happening during the manufacturing process, you can prevent potential damage to the equipment and fabric – helping you save cost in the longer run.
Now that you know what silicone defoamer is, let’s understand how they work in the context of textile manufacturing.
- How Does Silicone Defoamer Work in Textile Manufacturing?
Being in textile manufacturing, you must know how foam-related issues during dyeing, washing, and finishing processes can result in uneven coloration, reduced washing efficiency, and even machinery malfunctions, right?
Well, you can prevent all of these by using a silicone defoamer. The formulation of silicone defoamer lowers the surface tension between air bubbles and the liquid which results in the collapse of foam.
Moreover, the unique properties of silicone-based defoamers make them highly effective at dispersing bubbles in liquid solutions, such as dyeing vats, washing baths, and finishing agents.
To use silicone defoamers in textile manufacturing, you need to add them at various stages of production. By using silicone defoamers, you can make sure that the production process remains uninterrupted, reducing downtime and increasing efficiency.
The consistent performance of silicone defoamers also enhances product quality, as they ensure that textile fibers are processed without the interference of foam. And as a result, it improves textiles with better texture and consistency, making silicone defoamers a vital tool in high-quality textile production.
After knowing what silicone defoamer is and how that works in textile manufacturing, it’s obvious to wonder what the silicone defoamer manufacturing process looks like. Let’s find that out in the next paragraph.
- What Is the Silicone Defoamer Manufacturing Process?
There are many stages in the silicone defoamer manufacturing process. However, the main three stages are formulation, blending, and testing.
In the first stage of formulation, you need to have the right combination of siloxane-based compounds and emulsifiers to create a highly effective defoamer.
Once the formulation stage is done, there comes the stage of the blending process, where the ingredients are mixed thoroughly to achieve the desired consistency and performance.
Lastly, quality control is done to make sure that the defoamers are safe, effective, and environmentally friendly.
This whole silicone defoamer manufacturing process makes sure that the defoamers meet the required specifications for various textile applications while producing a consistent and high-quality product suitable for a wide range of textile processes.
With the kind of role silicone defoamers play in textile manufacturing, there’s no doubt that it has multiple benefits to offer!
Let’s have a look at the various advantages of silicone defoamer in the textile industry in the following paragraph.
- What Are the Key Benefits of Silicone Defoamer in Textile Manufacturing?
Silicone defoamer works like magic across all the stages of the textile manufacturing process with many benefits to offer as mentioned below:
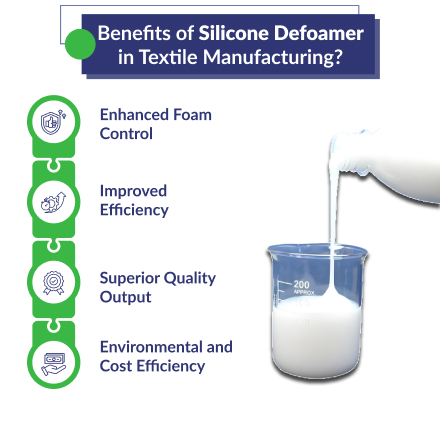
- Enhanced Foam Control:
The first and foremost benefit silicone defoamers have to offer in textile manufacturing is super effective foam control compared to all other traditional defoamers.
Their unique chemical structure allows them to effectively handle foam in a variety of textile processes.
And as the foam is highly controlled with a defoamer, it leads to a smoother and more efficient production process while reducing interruptions.
- Improved Efficiency:
Along with enhanced foam control, silicone defoamers also improve efficiency by reducing the downtime caused by excessive foam. Moreover, it also helps in reducing the frequency of maintenance schedules as there are fewer malfunctions being caused by foam creation.
The combination of reduced downtime and maintenance schedule allows you to meet production targets more easily and effectively.
- Superior Quality Output:
Silicone defoamers are not used only to reduce the hurdles of textile manufacturing but also to improve the quality of the products. By using silicone defoamers at various stages of textile production, you can achieve consistent quality across large batches.
Moreover, as silicone defoamers ensure even dye application, you can promise high-quality finished textiles with enhanced texture and appearance to your channel partners and customers.
- Environmental and Cost Efficiency:
If you are concerned about the silicone defoamer price, let us tell you that they are more cost-effective in the long run due to their efficiency. As they reduce the need for excessive cleaning and maintenance of machines, you need to spend less on operational costs.
Additionally, their effectiveness reduces the consumption of raw materials, contributing to environmental sustainability by minimizing waste in the production process.
With all the benefits silicone defoamers have to offer at the price it comes, we can definitely tell that they are a wise choice for you if you are a textile manufacturer.
- Why Choose Silicone Defoamer from Leading Manufacturers in India?
We are sure after knowing the role and benefits of silicone defoamers in the textile industry, you feel like contacting silicone defoamer manufacturers in India. Well, it’s a good idea but let us tell you that you should opt for the best ones only as they are reliable and can offer you more options than others.
As India is a leader in the production and export of high-quality silicone defoamers for textiles, you can find the best and most cost-effective without compromising on performance.
When you choose the best from the range of silicone defoamer manufacturers in India, you get the highest quality control as they adhere to global standards and offer a range of defoamers designed to suit various textile processes, from dyeing to washing.
- How Does Silicone Defoamer Price Affect Textile Manufacturers?
When you are comparing multiple silicone defoamer manufacturers in India, you may find the silicone defoamer price a little high. But let us tell you that this high upfront price can save you a lot in the long run with all the benefits they have to offer.
Moreover, there are several factors that influence the silicone defoamer price, including the raw materials used, production processes, and the scale of manufacturing.
If you decide to make bulk purchasing from leading silicone defoamer manufacturers in India, you can save significant costs. As the cost-benefit ratio of using silicone defoamers is highly favorable, it is definitely a smart investment choice for textile manufacturers like you.
- Colourinn – A Textile Auxiliaries & Chemicals Manufacturer for Your Silicone Defoamer Supply
There’s no doubt that silicone defoamers play an integral role in the textile industry by improving efficiency, reducing waste, and ensuring high-quality production. By choosing the right silicone defoamers, manufacturers can benefit from better foam control and improved productivity.
If you are looking for reliable silicone defoamer suppliers, consider the advantages of sourcing your defoamers from trusted manufacturers in India. These high-quality defoamers will ensure that your production processes run smoothly, delivering superior textile products every time.
Frequently Asked Questions
Q1. What is Silicone Defoamer?
A. Silicone defoamer is a chemical additive that can reduce or inhibit the formation of foam during the industrial process. This chemical is especially effective for textile applications in maintaining process efficiency and the quality of products.
Q2. Why does the textile industry use silicone defoamer?
A. By using silicone defoamers in textile processing, unwanted foam can be eliminated. This foam often prevents dyeing, printing, and finishing operations from running as smoothly as they could. It thereby makes for smoother operations and an end-product of uniform quality.
Q3. What is the action of Silicone Defoamer?
A. Silicone defoamers may reduce surface tension in foams, leading to the coalescence of bubbles, followed by collapse. This results in prevention of foam generation as well as maintaining stability in the process environment.