Excessive foam creates more than just aesthetic problems. It leads to uneven dyeing, jams machinery, wastes water and energy delays timelines – and huge financial and material losses.
This is where anti foaming agent is necessary. These agents solve problems without causing foam disruptions and ensure consistent quality and optimized production efficiency. In this article, we describe how anti-foaming agents improve textile processes, cost and quality of output across the textile applications.
Understanding Anti-Foaming Agents and Their Role
In textile manufacturing, liquid processes often generate foam due to the interaction of chemicals, air, and mechanical agitation. Foam can trap air bubbles on fabric surfaces causing defects and process inefficiencies.
An anti-foaming agent commonly known as a defoamer—is a chemical additive that prevents or reduces foam formation. By breaking down foam quickly or stopping it from forming altogether, anti-foaming agents stabilize processes and increase efficiency – whether in dye baths, printing machines or finishing lines.
Why is Foam a Problem in Textile Manufacturing?
Foam develops when surfactants, dyes or chemicals combine with air in high-speed agitation, or mechanical processes. The foam may be invisible but interferes with critical operations resulting in inefficiencies and quality issues. The main problems foam causes are:
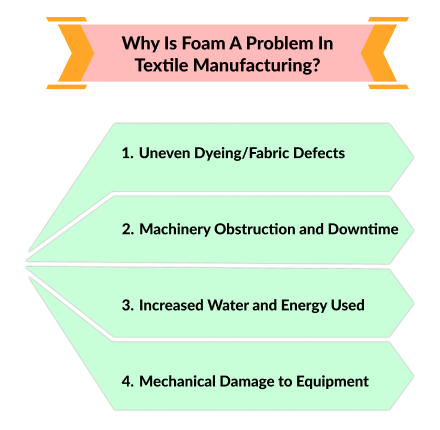
- Uneven Dyeing/Fabric Defects
Foam forms air pockets on the fabric surface during dyeing that prevent even distribution of dyes and chemicals. That creates patches of uneven colouring and decreases the aesthetic value of textiles. Such flaws would cause more rejection and material waste for producers who want to fulfil high-quality requirements.
- Machinery Obstruction and Downtime
In high-speed machinery, foam obstructs pipes, nozzles and filters, causing downtime and production loss. Machines sometimes have to be stopped completely to clean, which causes downtime and lost productivity. Frequent maintenance imposes additional operational costs and delivery time pressure.
- Increased Water and Energy Used
Trapped bubbles and chemical residues from foam-related disruptions may require additional rinsing and cleaning cycles. This not only wastes huge amounts of water but also more energy, raises production costs and decreases the sustainability of the plant.
- Mechanical Damage to Equipment
Foam causes cavitation in pumps – pressured air bubbles collapse and damage the pump walls and impellers. This eventually wears down and requires repairs or replacements.
Controlling foam effectively is critical for textile manufacturers to achieve smooth processes, maintain high-quality output, and ensure cost efficiency.
Key Benefits of Anti-Foaming Agents in Textile Manufacturing
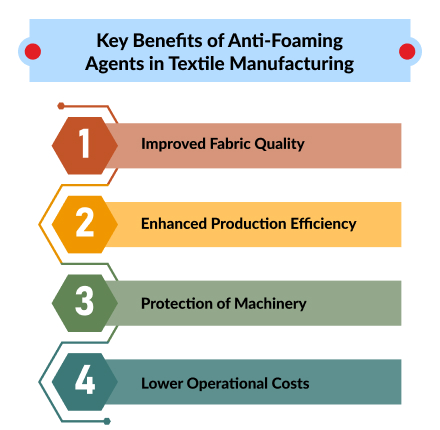
1. Improved Fabric Quality
Foam leads to poor finishing or uneven colour patches. Foaming agents blow out air bubbles to remove them so colour and chemicals can be applied to the fabric. This produces consistent industry standard quality output.
2. Enhanced Production Efficiency
Foam blocks high-speed textile machines and producers must stop production for maintenance or cleaning. A foaming compound shortens foam delays so equipment can work at maximum efficiency. So faster production gives more output and lower expenses.
3. Protection of Machinery
Foam buildup worsens the wear on the machinery. Cavitation or the collapse of air bubbles inside pumps, pipes and gear may result from it. Anti-foaming products reduce maintenance costs, equipment life and such risks.
4. Lower Operational Costs
Rinsing, downtime and maintenance of foam are additional costs. These inefficiencies are eliminated with anti-foaming agents that save water, energy and money on equipment repairs or replacements. The manufacturer might eventually save money.
Types of Anti-Foaming Agents
The types of anti-foaming agents help textile manufacturers choose the right solution for their process. These are:
1. Silicone-Based Antifoaming Agents
Anti-foaming agents containing silicon are among the most common because of their high efficacy, stability and versatility. These are a mixture of silicone oils and hydrophobic particles that perform best in aqueous systems like dye baths and washing.
Key Benefits:
- High Efficiency: Needs minimal dosage for best foam control.
- Temperature Stability: These are good over a wide temperature range and are therefore suitable for high-temperature dyeing.
- Non-Residue Forming: Produces clean, superior results with no residue on textiles.
- Chemical Compatibility: Works well with most dyes, finishes and surfactants.
Find out more benefits and applications of silicone defoamers in textile manufacturing. See our article for more on how these agents deal with foam problems. Read here: Benefits of Silicone Defoamer in Textile Manufacturing.
2. Non-Silicone Anti Foaming Agents
Such agents may contain natural ingredients, fatty alcohols, or mineral oils. These are suitable for procedures in which silicone residues may impair the chemical compatibility/quality of the final product.
Key Benefits:
- Oil-Based Applications: Particularly helpful for solvent-based treatments that use anti-foaming agents in oil systems.
- Eco-friendly: A few non-silicone agents are safe for use in sustainable production systems and biodegradable.
- Residue Control: Ideal for uses such pharmaceutical textile processes where silicone-free formulations are desired.
How to Choose the Right Anti-Foaming Agent
The best anti-foaming agent is dependent upon the textile process and operation. Consider the following factors:
- Process Compatibility: Verify that the anti-foaming agent works with the other chemicals in your production line.
- Dosage Requirements: Pick an agent that gives maximum efficacy at a minimum dosage to save costs.
- Residue and Staining: Anti-foamers should leave no residues that impair fabric quality.
Applications Beyond Textiles
Anti-foaming agents are needed in textile manufacturing but they also play a key role in other industries.
- Oil Industry: Foam may delay production in processes involving anti-foaming agents in oil. Defoamers assure continuous oil extraction and processing.
- Pharmaceuticals: Anti-foaming agent pharmaceutical applications prevent foam formation in drug formulations ensuring stability and accuracy during production.
Anti-foaming agents have an important industrial application outside of textiles. Read more on how these agents improve various industrial processes in How Antifoaming Agents Enhance Industrial Processes.
Conclusion: Why Anti-Foaming Agents Are Essential
Foam interrupts processes increases costs and compromises quality during dyeing and printing. Anti-foaming agents remove these difficulties, improve efficiency, and protect machinery & textile quality.
At Colurinn we understand how Anti-foaming agents play an extremely important role in textile production. View our range of quality anti-foaming agents for textile and allied industries. Let us make your production batches more efficient, quality and consistent.
Frequently Asked Questions
Q1. How are anti-foaming agents applied in textile processes?
A. They can be added directly to the processing bath or applied as part of a continuous system, depending on the process requirements.
Q2. How do anti-foaming agents work?
A. Anti-foaming agents break the surface tension of foam bubbles, causing them to collapse. They also prevent the formation of new foam by altering the liquid’s surface properties.
Q3. What are the types of anti-foaming agents used in textiles?
A. Common types include: Silicone-based agents: Effective across a wide range of conditions.
Non-silicone-based agents: Typically mineral oil or polymer-based.
Water-based agents: Suitable for eco-friendly processes.